Construction leaders are grappling with labor shortages, supply chain pressures and shifting policies entering 2025.
Labor remains a significant cost factor in the construction industry, particularly in regions with high-tech and mission critical projects, like data centers, said Jeff Peragallo, director and vice president of operations at construction consultancy Linesight. The Dublin-based firm recently released its Construction Markets Insights report, covering trends in labor, supply and materials pricing across the U.S.
While commodity prices have largely stabilized in 2024, fluctuating metal costs and ongoing procurement challenges continue to test the construction industry’s resilience.
Still, proactive planning and strategic investments can help contractors prepare for the year ahead. Here, Peragallo talks with Construction Dive about labor shortages, procurement strategies and the future of data center construction.
This interview has been edited for brevity and clarity.
CONSTRUCTION DIVE: What are the main takeaways from this report?
JEFF PERAGALLO: Labor remains a significant cost factor due to the shortage of skilled workers. Regions with significant high-tech and mission-critical projects still struggle with a lack of skilled labor, particularly in the MEP trades.
In 2024, demand for AI computing and data center expansion drove significant pressure on the supply chain, particularly in power and cooling solutions. While 2024 tested the resilience of supply chains, proactive planning and supplies investments provide hope for 2025.
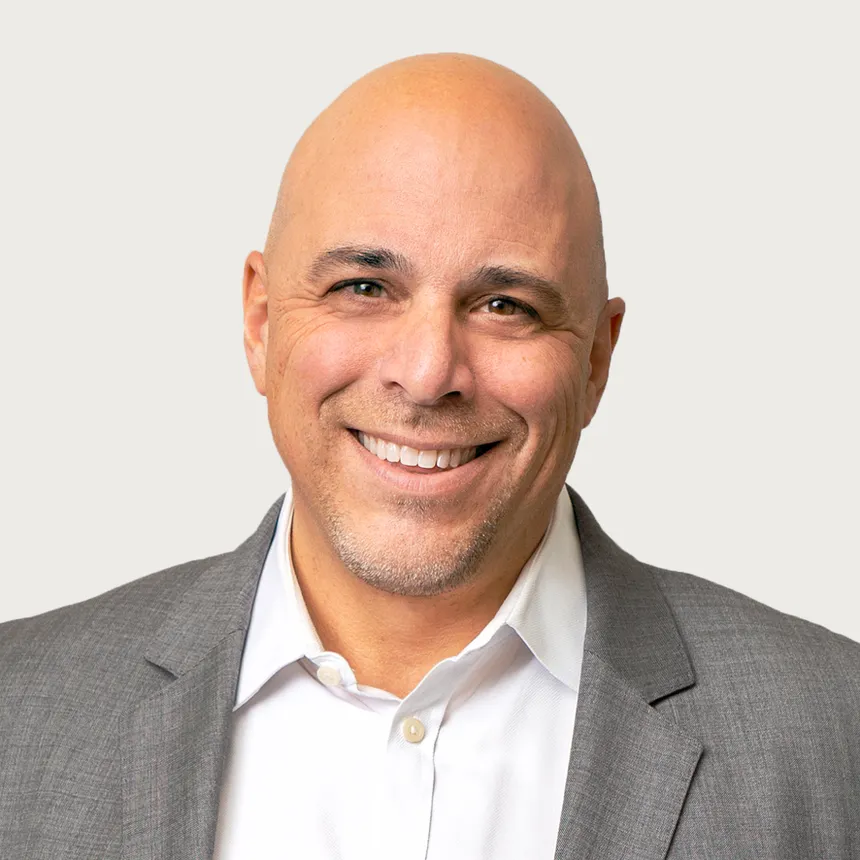
Jeff Peragallo
Courtesy of Linesight
During 2025, the new administration may introduce changes related to immigration policies and tariffs. This will require close monitoring. Additionally, while prices for most commodities have stabilized, the fluctuating price of metals remains a concern. Copper and aluminum prices are higher than they were in 2023 due to issues with supply, raw material availability and import costs.
Labor shortages remain a persistent problem in construction. What strategies or policy changes are top of mind in 2025 to mitigate some of this?
Several strategies are top of mind for 2025. Before commencing significant construction projects, a labor survey can provide critical insights into local construction supply and demand. This helps determine if the labor pool geography needs expansion or if other measures are required to secure adequate labor.
Offsite fabrication is another strategy. Reducing onsite labor requirements by leveraging offsite fabrication can significantly improve efficiency and address labor constraints.
Creating an appealing work environment is also essential. This includes providing onsite amenities, cultivating a positive jobsite culture and offering unique perks to attract and retain workers. Lastly, focus on partnerships and repeat business with vendors in the industry to create consistent and reliable resources versus an ongoing cycle of competitive bidding.
This approach can enhance project planning and execution, helping mitigate ongoing labor shortage challenges.
How should contractors approach procurement and pricing strategies to mitigate risks in 2025?
Early engagement with vendors and accurate demand forecasting are essential. Collaborating with vendors early in the project lifecycle ensures better access to production slots and allows contractors to lock in pricing before potential cost increases.
Next, expanding the supplier base reduces reliance on single sources, helping to manage risks associated with supply chain disruptions or geopolitical challenges. Monitoring commodity trends, such as fluctuating costs of materials, can help contractors make informed decisions on when and how to purchase materials. Leveraging price drops strategically can reduce costs, while also noting that price changes due to tariffs are excluded from proposals.
Contractors should also prioritize components with challenges in procurement, such as transformers and cooling systems, to avoid delays.
AI-driven data center demand has pressured supply chains, particularly for power and cooling solutions. How do you foresee this evolving in 2025, and what opportunities or challenges does it present for contractors?
2024 saw persistent challenges with long lead times for critical equipment, including generators over 3,000 kW facing lead times of up to 130 weeks globally and medium voltage transformers averaging 43 to 47 weeks in lead time.
AI computing and data center expansion put significant pressure on the power and cooling solution supply chain, with constrained supplier capacity impacting project timelines.
Relief from these efforts is expected in 2025, with opportunities to expand production capacities from key suppliers, which should begin to stabilize lead times in the second half of 2025. Cooling solutions and power distribution systems will be areas of focus, with ongoing innovation to meet growing demands.
However, the challenge will continue to be a high demand for advanced equipment and potential external disruptions, including geopolitical risks.
To mitigate risks, firms will need to strengthen demand forecasting, secure production slots early and diversify supplier bases. Early engagement with vendors and strategic forecasting will remain vital for navigating ongoing complexities.